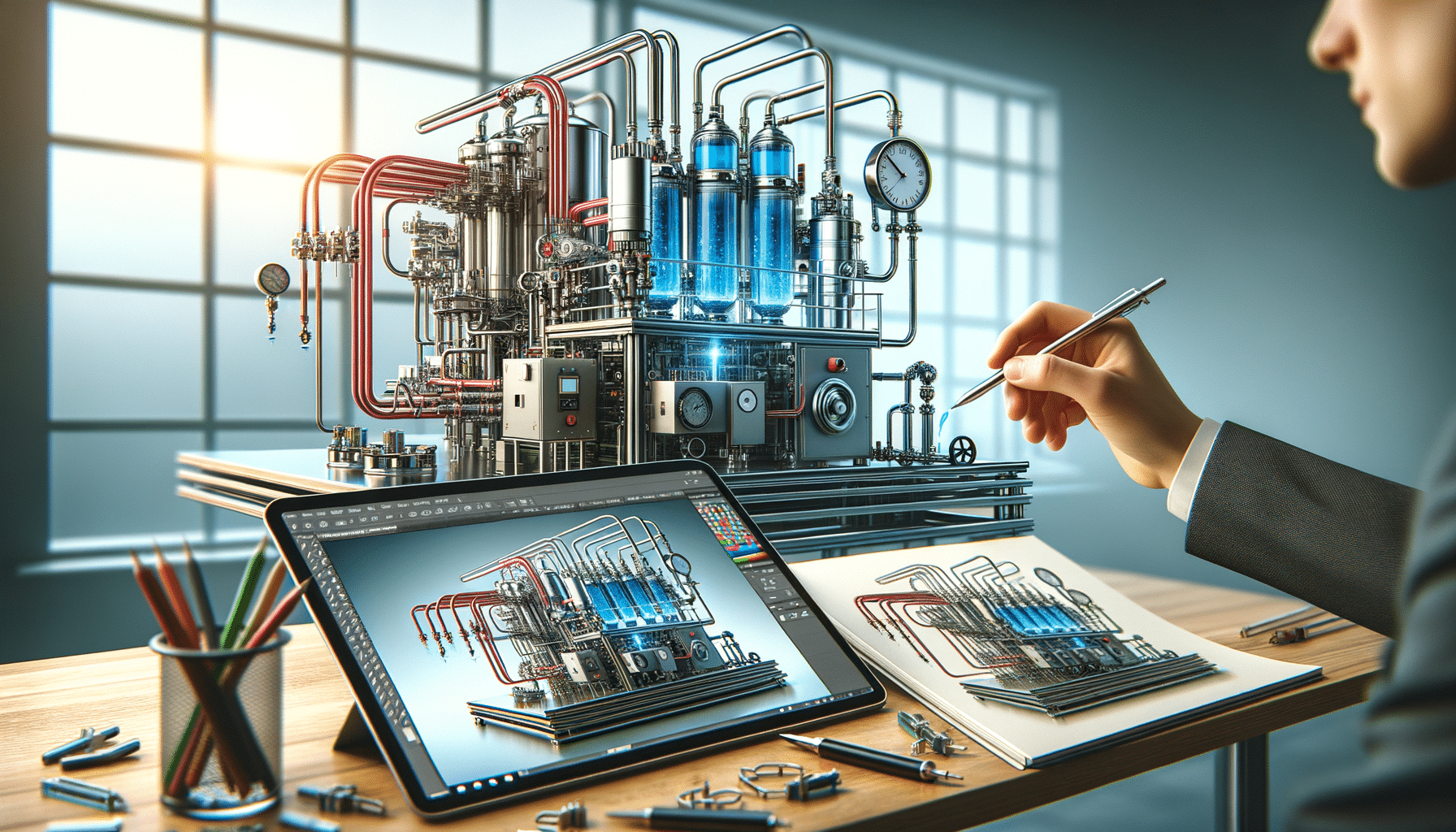
Introduction to Pneumatic Systems: Principles and Applications
Understanding Pneumatic Machines
Pneumatic machines are an integral part of modern industrial operations, utilizing compressed air to perform a variety of tasks. These machines convert the energy of compressed air into mechanical motion, offering a clean and efficient alternative to traditional power sources. The principles of pneumatics are based on the properties of gases and the force they exert when compressed. This fundamental concept has been harnessed to create machines that can lift, move, and manipulate objects with precision and speed.
The versatility of pneumatic systems is evident in their widespread application across industries. They are commonly found in manufacturing plants, automotive assembly lines, and even in the packaging industry. The reason for their popularity lies in their simplicity and reliability. Pneumatic systems are relatively easy to maintain and can operate in environments where electrical systems might pose a risk. Additionally, they offer a high degree of control, allowing for precise adjustments in speed and force.
Some of the key components of a pneumatic system include compressors, air tanks, valves, and actuators. Compressors are responsible for generating compressed air, which is then stored in air tanks. Valves control the flow of air to the actuators, which convert the air pressure into mechanical movement. This straightforward design makes pneumatic machines an attractive option for many industrial applications.
Pneumatic Batch Coding Machine
The pneumatic batch coding machine is a specialized application of pneumatic technology, designed to print batch codes, manufacturing dates, and other essential information on products. This machine is crucial for industries that require accurate and efficient marking of their products for traceability and compliance with regulations.
Batch coding machines operate by using compressed air to drive a printing mechanism. This method ensures that the printing process is both fast and reliable, capable of handling high-volume production runs. The use of pneumatics in batch coding machines offers several advantages, including reduced operational costs and minimal maintenance requirements. These machines are designed to work with a variety of surfaces, from paper and cardboard to plastic and metal, making them versatile tools in any production line.
One of the standout features of pneumatic batch coding machines is their adaptability. They can be easily integrated into existing production lines and can be configured to print different types of codes as needed. This flexibility is essential for manufacturers who need to comply with varying industry standards and customer requirements. The efficiency and precision of pneumatic batch coding machines make them a preferred choice for businesses seeking to enhance their production capabilities.
Advantages of Pneumatic Systems
Pneumatic systems offer a range of benefits that make them appealing to industries worldwide. One of the primary advantages is their safety. Since pneumatic systems use air as a medium, there is no risk of fire or explosion, making them ideal for hazardous environments. Additionally, pneumatic systems are easy to install and maintain, with fewer moving parts compared to hydraulic or electrical systems.
Another significant benefit is their energy efficiency. Pneumatic systems can operate continuously without overheating, reducing downtime and increasing productivity. They also offer a high power-to-weight ratio, meaning they can deliver substantial force without being bulky. This makes them suitable for applications where space is limited.
Pneumatic systems also provide excellent control over speed and force, allowing for precise operations. This level of control is crucial in industries where accuracy is paramount. Furthermore, the components of pneumatic systems are generally less expensive than those of hydraulic systems, offering cost savings in both initial setup and long-term maintenance.
Applications of Pneumatic Technology
The application of pneumatic technology extends beyond industrial manufacturing. In the medical field, pneumatic systems are used in devices such as ventilators and other life-support equipment. The precision and reliability of pneumatics make them suitable for sensitive applications where human lives are at stake.
In the automotive industry, pneumatic tools are used for tasks such as tire inflation, brake systems, and suspension systems. The ability to deliver consistent and controlled force makes pneumatics an invaluable asset in automotive manufacturing and maintenance.
Pneumatics are also employed in the construction industry, powering tools such as jackhammers and nail guns. The robustness and durability of pneumatic tools make them ideal for demanding construction environments. Additionally, pneumatic systems are used in the packaging industry for tasks such as sealing, labeling, and filling, where speed and accuracy are essential.
Future Trends in Pneumatic Systems
As industries continue to evolve, so too do pneumatic systems. Innovations in materials and technology are leading to more efficient and environmentally friendly pneumatic systems. One trend is the development of smart pneumatics, which incorporate sensors and connectivity to enhance performance and provide real-time data monitoring.
Another trend is the integration of pneumatics with other technologies, such as robotics and automation. This combination allows for the creation of sophisticated systems that can perform complex tasks with minimal human intervention. The use of pneumatics in automated systems is expected to grow as industries seek to improve efficiency and reduce labor costs.
Furthermore, advancements in energy storage and compressor technology are making pneumatic systems more sustainable. The focus is on reducing energy consumption and minimizing environmental impact, aligning with global efforts to promote sustainability in industrial operations.